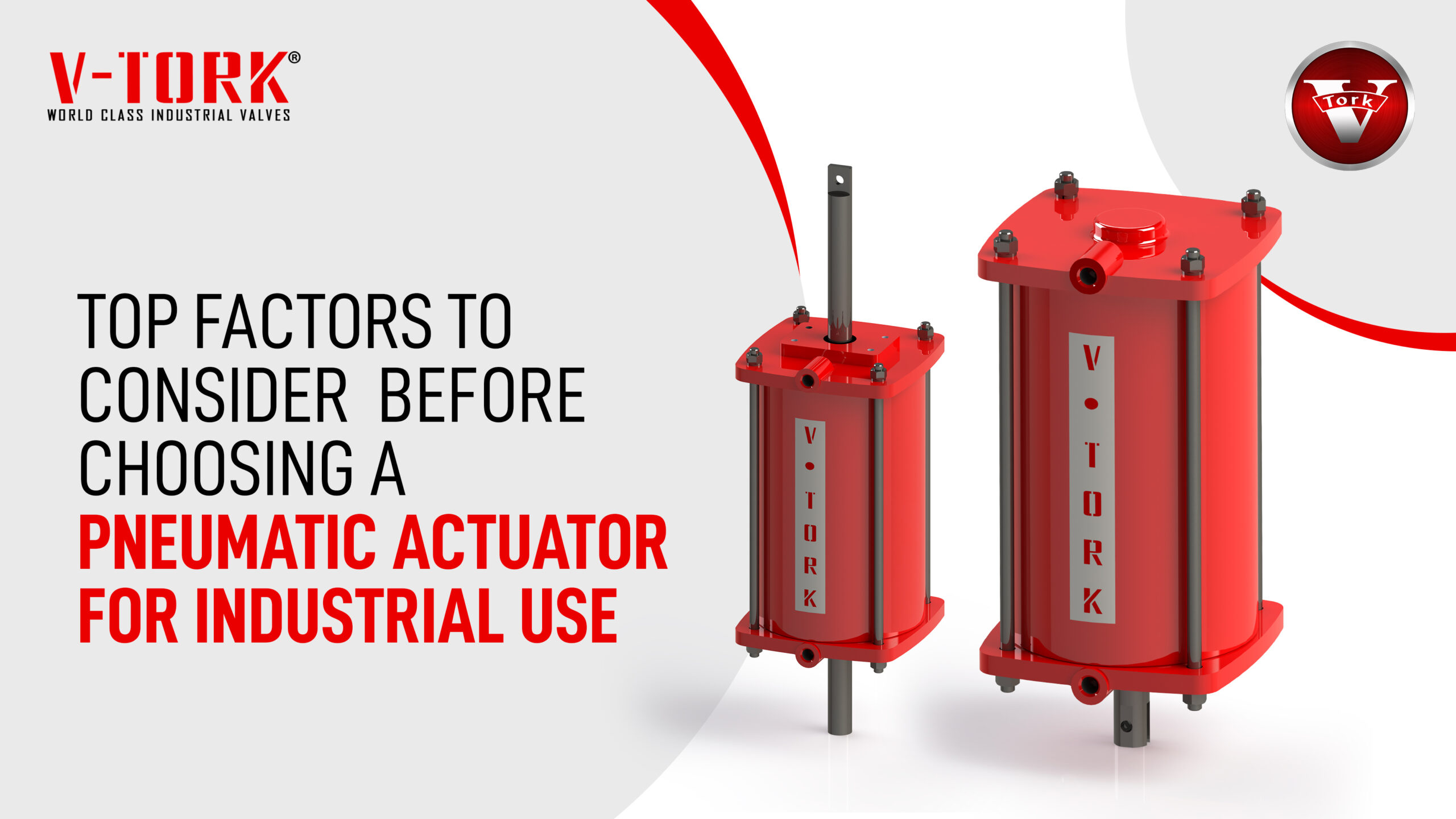
Top Factors to Consider Before Choosing a Pneumatic Actuator for Industrial Use | V-Tork Controls
In the fast-paced industrial setting of today, automation is the key to gaining optimum performance, minimizing the involvement of people and maintaining accurate control. Pneumatic actuators are the fundamental unit of many automated valve operations. Both in generation units or chemical processing units, be it gas control or valve operation, companies use them extensively to provide maximum operational efficiency.
When there are so many different types available, it is extremely important to find the best fit for your application. You need to consider several things, from understanding the pneumatic actuators’ working principle to matching them up with appropriate valve types like pinch valves, ball valves, or butterfly valves, before making the best decision.
What are Pneumatic Actuators?
Pneumatic actuators are automatic devices that open and close valves or dampers by transforming compressed air into mechanical motion. Industries and commercial processes widely use them where they require automation , particularly where installing hydraulic or electric systems may not be suitable in light of safety or environmental factors.
They exist in many forms from plain piston-operated to more involved rotary models. They are preferred for their quick response, low maintenance requirements, and cheap operation.
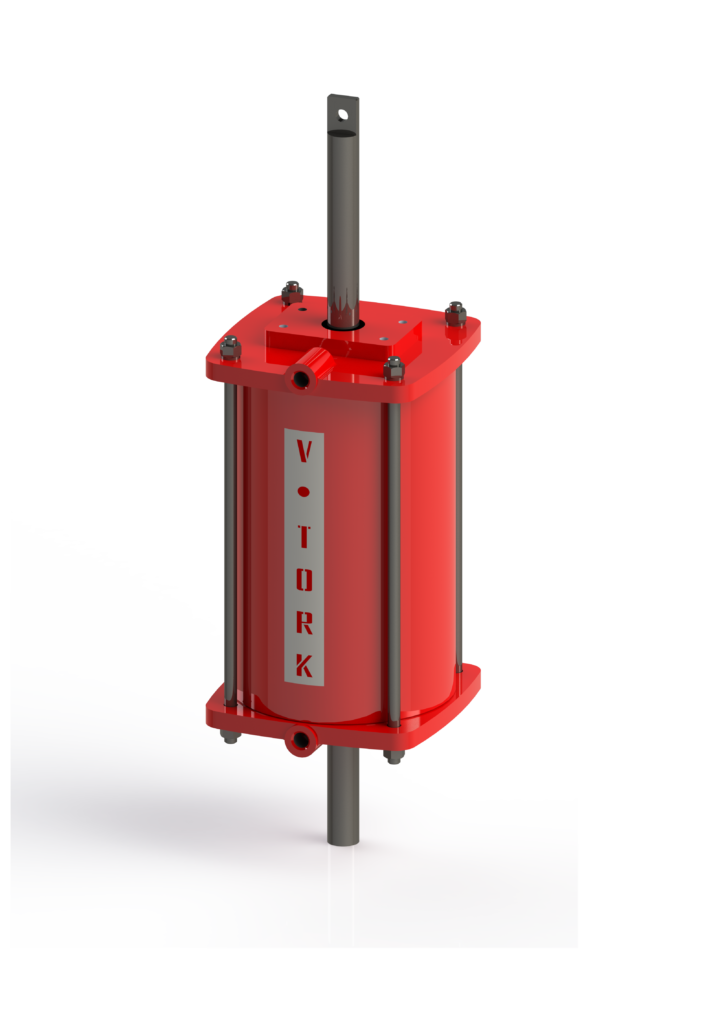
Pneumatic Actuator | V-Tork Controls
Working Principle of Pneumatic Actuators
To make the right decision, understanding how the working is a must. The working principle is based on the energy conversion of compressed air to rotary or linear motion. This is further utilized to open or close a valve or damper.
Compressed air powers a piston in a cylinder in linear actuators, which creates motion in one direction directly. Pressure from air produces rotary motion in rotary actuators. Actuators are designed to deliver fast and predictable motion. Many models include fail-safe spring return systems that activate in emergencies.
-
Nature of the Valve
Valves and actuators are not similar and neither are ball valves. Prior to actuator selection, it’s always good to match it against the exact valve type:
-
Ball Valves – Typically use quarter-turn rotary actuators. Their quick operating action is ideally suited to pneumatic rotary actuators.
-
Butterfly Valves – Are ideally suited to rotary actuators as they operate on a 90-degree turn.
-
Gate Valves – Typically use linear actuators, particularly in large systems where more stroke is needed to open the gate.
-
Pinch Valves – When dealing with slurries or aggressive fluids, they are typically utilized with specific linear actuators that provide non-contact action.
Smooth operation, avoidance of overloading, and optimal system life are guaranteed through proper combination.
-
-
Types of Pneumatic Actuators
There are two pneumatic actuator types which are used in industries:
-
Linear Pneumatic Actuators – These produce motion in a linear direction and are appropriate for gate valves, pinch valves, and control dampers.
-
Rotary Pneumatic Actuators – These offer quarter-turn or multi-turn rotary motion to find standard application with ball or butterfly valves.
Some utilize scotch yoke or rack and pinion mechanisms to transform linear air pressure to rotary motion.
V-Tork Controls has supplied over 10,000 pneumatic linear actuators (cylinders) to clients like NTPC, BHEL, and other PSUs. These products have proven reliable and have gained wide industrial acceptance.
-
-
Operating Conditions
Environmental and operational conditions significantly impact actuator selection. Consider the following:
-
Temperature Range – These actuators should be capable of operating in the temperature extremes expected in your application.
-
Corrosive Environments – Use actuators with protective coatings or made from corrosion-resistant materials.
-
Explosion Hazard Areas – These actuators are ideal for these settings since they don’t generate sparks, unlike electric actuators.
Always ensure that the selected actuator meets industry safety and compliance standards for your specific environment.
-
-
Required Torque or Force
Each valve type and size requires a specific amount of torque (for rotary actuators) or force (for linear actuators) to operate effectively. Undersized actuators may fail to operate the valve under pressure, while oversized actuators may result in excessive wear or inefficient energy use.
Consult valve datasheets and consider factors such as line pressure, valve size, and operating frequency to determine the correct actuator sizing. -
Control Method and Automation Needs
-
On/Off Control – Simple applications like shut-off valves.
-
Modulating Control – For processes that require precise flow adjustments, use actuators with positioners or proportional control.
-
Fail-Safe Operation – In critical applications, choose actuators with spring-return mechanisms. These ensure the valve closes (or opens) during power failure.
For enhaned process control, they can also be integrated with smart positioners and sensors.
-
-
Maintenance and Reliability
These are generally low maintenance, but selecting a robust, proven design is crucial for ensuring long-term reliability. Look for:
-
Sealed components to prevent dust and moisture ingress
-
Durable seals and wear-resistant parts
-
Easy access for periodic servicing
Trusted brands like V-Tork Controls offer high-quality actuator solutions. They help reduce unplanned downtimes and boost overall productivity in demanding industries.
-
-
Applications of pneumatic actuators
The applications span a wide range of industries due to their versatility, responsiveness, and cost-effectiveness:
-
Power Plants – For steam isolation, boiler control and flow regulation.
-
Oil & Gas – Used in explosive environments for safe valve automation.
-
Water Treatment – For regulating valves in filtration and chemical dosing systems.
- Pharmaceutical – Precision and safety in critical process controls.
-
Food & Beverage – Clean operation with minimal contamination risk.
In each of these industries, choosing the correct actuator plays a vital role in ensuring consistent and safe operations.
-
Final Thought
To conclude, selecting the right pneumatic actuator isn’t just about matching air pressure to movement. It involves a holistic evaluation of application needs, valve compatibility, environmental challenges, and long-term reliability. By understanding the working principle, identifying suitable types, and considering specific applications, you can ensure optimal performance and minimal downtime. Companies like V-Tork Controls have made significant contributions to India’s industrial automation landscape.
So, when you’re evaluating actuator options, start with automation in mind. Often, pneumatic actuators lead the way.