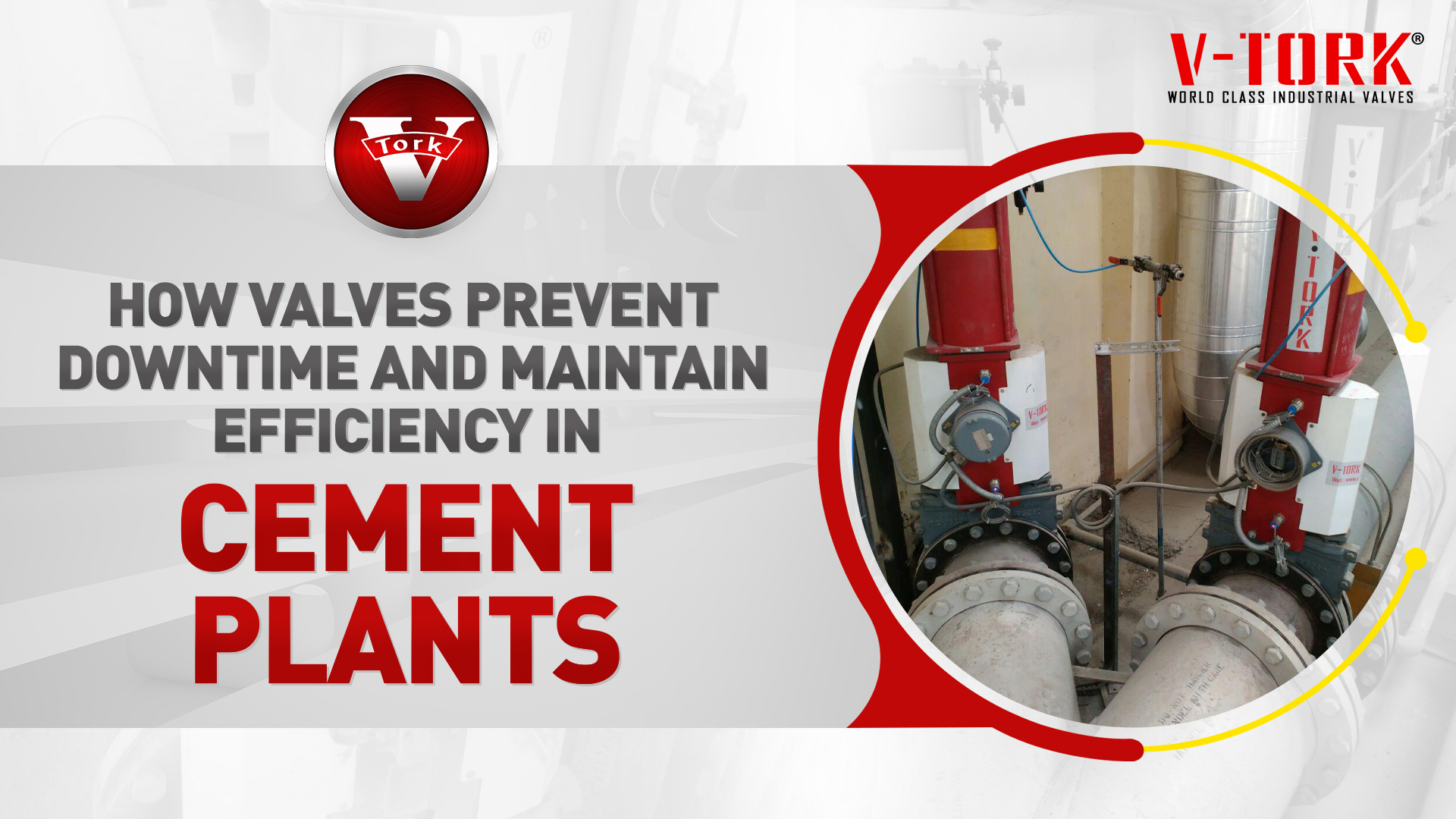
How Valves Prevent Downtime and Maintain Efficiency in Cement Plants
Cement production is a complex and continuous process, where even a minor disruption can lead to significant downtime and lost revenue. In this intricate dance of machinery and materials, valves play a crucial role as the silent guardians of efficiency. These unsung heroes regulate the flow, pressure, and direction of various substances throughout the entire production line, preventing issues and ensuring smooth operation.
Understanding the Cement Production Process: A Journey of Transformation
To fully appreciate the importance of valves, let’s take a brief journey through the key stages of cement production:
Raw Material Handling: Crushed limestone, clay, and other raw materials are transported and stored in silos. Valves regulate the flow of these materials into feeders before grinding.
Grinding: Raw materials are ground into a fine powder called “meal” using grinding mills. Valves control the flow of meal into the mills and ensure proper air circulation for efficient grinding.
Kiln Operations: The prepared meal is fed into a rotary kiln, where it undergoes high-temperature calcination to form clinker, the main component of cement. Valves regulate the flow of meal into the kiln and control the injection of fuel (coal, gas) to maintain the desired temperature.
Clinker Grinding: Produced clinker is then ground with additives like gypsum to create the final cement product. Valves control the flow of clinker and additives into grinding mills, ensuring proper mixing and particle size distribution.
Storage and Distribution: Finished cement is stored in silos before being transported to customers. Valves control the flow of cement during loading and unloading operations.
The Silent Guardians at Work: How Valves Prevent Downtime
Now, let’s explore how valves specifically contribute to minimizing downtime and maintaining efficiency in cement plants:
Leak Prevention: Leaks can be disastrous in a cement plant. Faulty valves can lead to leaks of raw materials, fuel, or even clinker, causing material loss, production delays, and environmental concerns. Properly functioning valves with reliable seals prevent leaks and ensure smooth flow throughout the process.
Maintaining Flow Control: Cement production relies on precise flow control of various materials. Valves regulate the flow of raw materials into feeders and grinding mills, ensuring consistent feed rates for efficient processing. Similarly, valves control fuel injection into the kiln and air circulation, maintaining optimal conditions for calcination.
Preventing Blockages: Uncontrolled flow can lead to blockages in pipelines or equipment. Valves help ensure proper flow distribution and prevent blockages by regulating material flow and preventing air intake issues.
Facilitating Maintenance: Certain valves, like isolation valves, allow for isolating specific sections of the production line for maintenance purposes. This minimizes downtime by allowing targeted repairs without shutting down the entire plant.
Choosing the Right Valve for the Job
Different stages of cement production require valves with specific functionalities and material compatibility. For example, high-temperature resistant valves are crucial for kiln operations, while abrasive-resistant valves are better suited for handling raw materials. By carefully selecting valves based on pressure rating, temperature requirements, and material handling needs, cement plants can ensure reliable performance and minimize downtime due to valve failures.
Beyond Prevention: Valves for Enhanced Efficiency
Valves contribute to efficiency beyond just preventing downtime. Precise flow control allows for optimal utilization of raw materials and fuel throughout the production process. By regulating the flow of materials into feeders and mills, valves ensure there’s neither an excess nor a shortage – minimizing waste and maximizing production output. Similarly, valves control the flow of air and fuel injection into the kiln, leading to more efficient use of energy during calcination. Finally, maintaining consistent flow and proper air circulation throughout the process using reliable valves contributes to consistent product quality. This translates to a more efficient and cost-effective operation for cement plants.
Partnering for Peak Performance: V-Tork’s Commitment to Cement Production
V-Tork understands the unique challenges faced by cement plants. We offer a comprehensive range of high-performance valves specifically designed for this demanding environment. These valves are built tough, utilizing durable and abrasion-resistant materials to withstand the wear and tear from abrasive materials. Additionally, V-Tork Controls offers high-temperature resistant valves for the extreme heat encountered in kiln operations.
Our commitment extends beyond the valves themselves. Many V-Tork Controls valves incorporate features that simplify maintenance procedures, minimizing downtime and ensuring smooth operation. V-Tork Controls also offers expert support, partnering with cement plants to create a customized solution for their specific flow control needs. This includes valuable expertise in valve selection and application advice. Together, V-Tork Controls valves and a proactive maintenance plan can help cement plants achieve a reliable flow control system that minimizes downtime, optimizes production efficiency, and ultimately leads to a successful and profitable operation.